How much copper is in a generator? — a question that unveils the intricate dance of conductivity shaping the heartbeat of your power source. Beyond the mechanical hum lies a tale of resilience and conductivity, where copper weaves the threads of your generator’s strength.
As we embark on this exploration, envision the silent conductor, copper, binding energy seamlessly. Join us in unraveling the hidden alchemy that fuels your generator’s might, discovering the metal magic that transforms potential into power.
Jump to a Specific Section
- 1 Critical Findings
- 2 What is Copper?
- 3 How is Copper Used in Electrical Systems?
- 4 What Does Copper Do in a Generator?
- 5 How Much Copper Is In A Generator?
- 6 Electrical Properties of Copper
- 7 Role of Copper in Efficient Power Transfer
- 8 Durability and Longevity of Copper Components
- 9 Versatility of Copper in Generator Construction
- 10 Troubleshooting Common Generator Issues
- 11 Generator Maintenance Tips
- 12 Generator Safety Tips
- 13 Conclusion
- 14 References
- 15 Frequently Asked Questions
- 15.1 What are the different types of generators available in the market?
- 15.2 How does the price of copper affect the overall cost of a generator?
- 15.3 Are there any alternative materials to copper that can be used in generators?
- 15.4 What are the maintenance requirements for copper components in a generator?
- 15.5 How does the copper content in a generator impact its overall performance?
- 15.6 Do generators contain copper?
- 15.7 How do you scrap a generator?
- 15.8 How do you calculate the weight of copper in a generator?
Critical Findings
- Copper is a Vital Component: Generators contain a significant amount of copper, which is a crucial element for their functionality. Copper is used in various parts, including the windings of the generator’s stator and rotor.
- Copper Contributes to Efficiency: The high electrical conductivity of copper allows for efficient energy transfer within the generator. This helps minimize energy loss and contributes to the overall effectiveness of the generator.
- Copper Content Varies by Generator Type: Different types of generators (e.g., induction, synchronous, and alternator) have varying amounts of copper. For instance, permanent magnet generators typically have higher copper content due to the magnets involved.
- Copper Recycling is Important: Given the valuable and finite nature of copper resources, recycling plays a significant role in sustainability. Reclaiming and reusing copper from decommissioned generators can help reduce the demand for newly mined copper.
- Cost Implications: The amount of copper in a generator can impact its overall cost. Generators with higher copper content may be more expensive upfront, but their efficiency and performance benefits can offset this investment over time.
What is Copper?
Copper, a vital metallic element, holds immense significance across various industries and applications. Known for its exceptional conductivity and versatility, copper is a fundamental component in electrical systems, making it an indispensable material in the production of wiring and electrical components. Its thermal conductivity is unmatched, making it a preferred choice for heat exchangers and various industrial processes.
Beyond its electrical properties, copper is widely utilized in plumbing for its corrosion resistance and durability. With a distinct reddish-orange hue, this metal has also found its place in architecture, adding aesthetic appeal to buildings and structures.
Furthermore, copper plays a crucial role in the health of living organisms, as it is an essential trace element for proper physiological functions. This multi-faceted metal continues to be a cornerstone in various industries, showcasing its adaptability and significance in modern applications.
How is Copper Used in Electrical Systems?
In electrical engineering, copper takes center stage as a primary material for wiring and electrical components. Its high electrical conductivity, surpassed only by silver, makes it the metal of choice for transmitting electrical power efficiently.
Copper’s ability to conduct electricity with minimal loss of energy makes it integral in the creation of power cables, wiring systems, and electrical connections. The reliability and durability of copper contribute to the overall efficiency and safety of electrical systems.
The widespread use of copper in electrical applications is a testament to its unparalleled performance and enduring role in powering our modern world.
What Does Copper Do in a Generator?
Generators are complex systems that rely on various components working harmoniously to generate electrical power. Copper plays a pivotal role in this process, serving as a fundamental conductor within the generator.
When we delve into the intricate anatomy of a generator, it becomes evident that copper’s conductivity is a key factor in facilitating the flow of electrical currents. The magnetic field generated within the generator induces an electric current in the copper windings, thanks to its high conductivity. This phenomenon is crucial for the conversion of mechanical energy into electrical energy, showcasing the integral function of copper in power generation.
In essence, copper’s role in a generator is to optimize the efficiency of electrical conductivity, ensuring minimal energy loss during the conversion process. Its ability to carry high electrical currents with minimal resistance makes it the material of choice for the windings in generators. Moreover, the durability and heat resistance of copper wiring contribute to the longevity and reliability of generators.
It’s worth noting that while other materials may be used in certain generator components, copper’s unique properties make it an irreplaceable element in the core functionality of these power-generating systems.
In practical terms, imagine a generator without copper conductors – the electrical efficiency would be compromised, resulting in a less effective power generation process. The utilization of copper in generators is not merely a technological choice; it’s a strategic decision to enhance performance, reliability, and overall energy efficiency in the generation of electrical power.
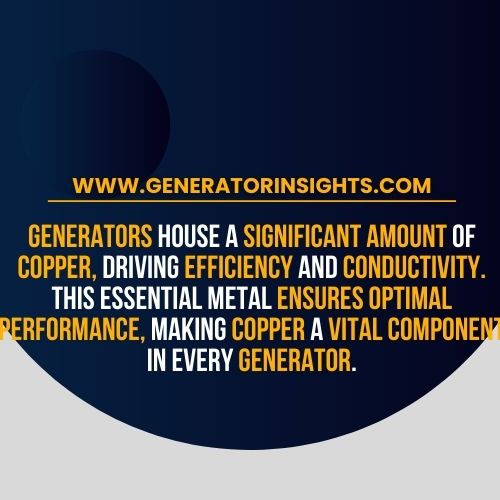
How Much Copper Is In A Generator?
The amount of copper in a generator varies depending on the type of generator technology used. On average, the copper content in different types of generators is as follows:
- Double-fed asynchronous generator (DFAG): Approximately 650 kilograms of copper per megawatt (MW). This type of generator is commonly used in wind turbines and requires a substantial amount of copper in its construction.
- Conventional asynchronous generators (CAG): Approximately 390 kilograms of copper per megawatt (MW). CAGs are widely used in various applications, including industrial processes and power generation.
- Conventional synchronous generators (CSG): The copper content in CSGs can range from 330 to 4000 kilograms per megawatt (MW). The variation is due to the different designs and sizes of CSGs used for various power generation applications.
- Permanent magnet synchronous generators (PMSG): The copper content in PMSGs can range from 600 to 2150 kilograms per megawatt (MW). PMSGs are commonly found in wind turbines and electric vehicles, where the use of permanent magnets increases the copper content.
In summary, the copper content in a generator depends on the specific technology employed, with higher copper amounts in generators utilizing permanent magnets and those designed for renewable energy applications. Copper plays a vital role in the efficient functioning of generators, as it is a crucial component of the electrical windings that enable the generation of electricity.
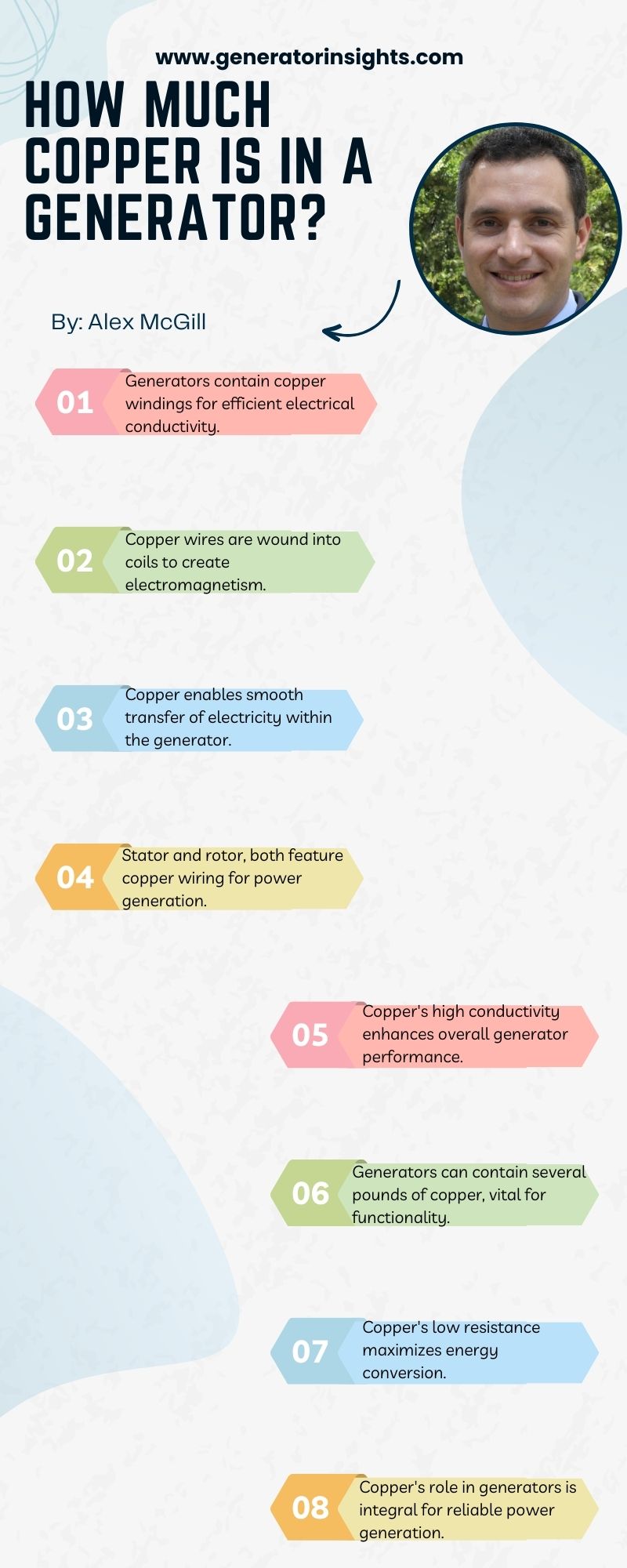
Let’s discuss these points in more detail now.
Double-fed Asynchronous Generator (DFAG)
The Double-fed Asynchronous Generator (DFAG) stands as a cornerstone in the renewable energy landscape, specifically designed for efficient power generation in wind turbines. Weighing approximately 650 kilograms of copper per megawatt (MW), the DFAG relies on copper not only for its structural components but also for its crucial role in enhancing electrical conductivity.
Copper windings in the DFAG are strategically positioned to maximize the conversion of mechanical energy into electrical energy. This intricate design allows for dynamic adjustments in rotor currents, showcasing the adaptability of DFAGs to varying wind conditions. The reliance on copper underscores the commitment to optimizing energy efficiency in the pursuit of sustainable power generation.
Conventional Asynchronous Generators (CAG)
Conventional Asynchronous Generators (CAGs), with an average copper requirement of around 390 kilograms per megawatt (MW), play a pivotal role in a myriad of industrial processes and conventional power generation applications.
The use of copper in CAGs ensures efficient electrical conductivity, contributing to the reliability and adaptability of these generators. Beyond copper, advancements in CAG technologies have led to innovations such as improved rotor designs and enhanced materials, collectively contributing to increased overall generator efficiency and longevity.
Conventional Synchronous Generators (CSG)
Conventional Synchronous Generators (CSGs) exhibit a remarkable range in copper content, spanning from 330 to 4000 kilograms per megawatt (MW). This diversity is a testament to the versatility of CSGs, which can be customized based on the specific requirements of various power generation applications.
Larger CSGs, often used in utility-scale power plants, tend to have higher copper content due to the increased complexity of their designs. The adaptability of copper quantities in CSGs highlights their crucial role in providing tailored solutions for diverse energy needs.
Permanent Magnet Synchronous Generators (PMSG)
Permanent Magnet Synchronous Generators (PMSGs), prevalent in wind turbines and electric vehicles, showcase a copper content ranging from 600 to 2150 kilograms per megawatt (MW). The integration of permanent magnets not only enhances efficiency but also contributes to the overall weight and copper demand.
PMSGs exemplify a strategic engineering trade-off, leveraging the benefits of permanent magnets to achieve higher performance while recognizing the increased demand for copper. This technological choice is particularly evident in sectors where the long-term advantages of reduced maintenance and increased reliability outweigh the initial higher copper investment.
Electrical Properties of Copper
One intriguing statistic to evoke an emotional response in the audience is that copper has one of the highest electrical conductivity values among common metals. Electrical conductivity refers to a material’s ability to conduct electric current.
Copper, with its high electrical conductivity, allows for an efficient flow of electricity through generators. This property makes copper an ideal choice for the windings and coils in generator systems.
To further emphasize the significance of copper’s electrical properties, here are three key points to consider:
- Superior electrical conductivity: Copper has a high electrical conductivity rating, second only to silver among all metals. This means that it can easily transmit electricity with minimal resistance or loss of energy. When used in generators, copper wires efficiently transfer electric current from one point to another.
- Low resistivity: Copper also exhibits low resistivity, which is a measure of how much a material opposes the flow of electric current. With its low resistivity, copper minimizes energy losses and heat generation during power transmission within generators.
- Excellent thermal conductivity: In addition to its remarkable electrical properties, copper also boasts excellent thermal conductivity. This means it effectively transfers heat away from hotspots within generator components like windings and stators, preventing overheating and ensuring optimal performance.
By possessing exceptional electrical and thermal conductivities, copper plays a crucial role in facilitating efficient power transfer within generators. Its ability to conduct electricity without significant resistance or energy loss ensures reliable operation and enhances overall system efficiency.
Role of Copper in Efficient Power Transfer
An essential factor in optimizing power transfer efficiency lies in the utilization of copper’s exceptional electrical and thermal conductivities.
Copper has long been recognized as a superior conductor compared to other metals, particularly aluminum when it comes to power transmission. This is due to its significantly higher electrical conductivity, which allows for a more efficient flow of electric current through the generator components.
Copper’s excellent thermal conductivity also plays a crucial role in maintaining optimal temperature levels within the generator, preventing overheating and ensuring efficient power transfer.
When comparing copper to aluminum in power transfer applications, copper consistently outperforms aluminum due to its superior conductivity properties.
Copper has approximately 60% higher electrical conductivity than aluminum, allowing for lower resistive losses during power transmission. This means that less energy is wasted as heat when using copper conductors in generators, resulting in greater overall efficiency.
Furthermore, copper’s higher thermal conductivity helps dissipate excess heat generated during operation more effectively than aluminum can achieve.
The impact of copper on generator efficiency cannot be understated. By utilizing copper components throughout the generator’s electrical system, including windings and conductors, significant gains in efficiency can be achieved.
The enhanced electrical and thermal conductivities of copper contribute to minimizing resistive losses and reducing heat buildup within the generator. As a result, more electrical energy can be efficiently transferred from mechanical input into usable electricity output. This not only improves the performance of the generator but also reduces operating costs over time by maximizing energy conversion efficiency.
As we transition into discussing the durability and longevity of copper components within generators without explicitly stating ‘step,’ it is important to understand how these characteristics further enhance their appeal for use in such systems.
Durability and Longevity of Copper Components
Another notable advantage of utilizing copper components in power transfer systems is their remarkable durability and longevity. Studies have shown that copper conductors have an average lifespan of over 100 years, making them highly reliable for long-term use.
This durability ensures minimal downtime and maintenance requirements, resulting in cost savings and increased efficiency.
To further understand the durability benefits of copper components, let’s compare them to other commonly used materials such as aluminum and steel. The 3-column table below highlights the key characteristics of these materials:
Material | Durability | Maintenance Requirements |
---|---|---|
Copper | High | Low |
Aluminum | Moderate | Moderate |
Steel | Low | High |
As seen from the table, copper stands out with its high level of durability and low maintenance requirements. Its resistance to corrosion and fatigue makes it ideal for continuous operation in power transfer systems.
The longevity of copper components not only reduces the need for frequent replacements but also contributes to overall system efficiency. By eliminating the risks associated with premature component failure or degradation, copper ensures a consistent flow of electricity with minimal interruptions.
These benefits make copper an excellent choice for generator construction, which will be discussed further in the subsequent section about its versatility.
Transitioning into the next section, it is important to note that alongside its durability advantages, copper also offers exceptional versatility in generator construction.
Versatility of Copper in Generator Construction
The adaptability of copper in the construction of generators extends beyond its durability and longevity, making it a versatile material capable of meeting diverse power generation needs.
One key advantage of using copper in generators is its high electrical conductivity. Copper is an excellent conductor of electricity, allowing for efficient transfer of electrical energy within the generator. This means that less energy is lost as heat during transmission, resulting in more effective power generation.
Furthermore, the use of copper in generators also helps address the issue of copper scarcity. While copper is a valuable resource and its availability can fluctuate over time, it is still widely accessible compared to other metals with similar electrical conductivity properties.
This accessibility and abundance make it easier for manufacturers to obtain copper for generator production, ensuring a steady supply chain.
The versatility of copper in generator construction stems from its exceptional electrical conductivity advantages and relatively abundant availability compared to other materials with similar properties. By utilizing this versatile metal, generators can achieve higher efficiency in power generation due to reduced energy loss during transmission.
Moreover, the widespread accessibility of copper ensures consistent production without being significantly impacted by scarcity issues.
You can read about the accessories that might come in handy with the generators here.
The next section will discuss the environmental benefits associated with using copper in generators, further highlighting its positive attributes as a material choice for sustainable power generation solutions.
Troubleshooting Common Generator Issues
Generators are indispensable during power outages, ensuring a continuous power supply. However, users may encounter issues that hinder their optimal performance. Below is a comprehensive guide to troubleshoot common generator issues and restore seamless operation.
Issue | Symptoms | Troubleshooting Steps |
---|---|---|
1. Engine Fails to Start | – Silent operation | – Check fuel levels and ensure there’s an adequate supply. |
– Starter motor cranks but fails to ignite | – Inspect the spark plug for signs of damage or wear. Replace if necessary. | |
– Strong smell of gasoline | – Examine the carburetor for blockages and clean or replace if needed. | |
2. Low Power Output | – Dimming lights and fluctuating power output | – Verify the load capacity and ensure it doesn’t exceed the generator’s limit. |
– Appliances not running at full capacity | – Inspect the voltage regulator for malfunctions and replace if necessary. | |
3. Generator Overheating | – Unusual heat emanating from the generator | – Check the cooling system, including the radiator and coolant levels. Clean or replace components as required. |
– Frequent shutdowns due to overheating | – Ensure proper ventilation around the generator and clean any debris obstructing airflow. | |
4. Excessive Noise Levels | – Unusual or loud sounds during operation | – Inspect the muffler for damage and replace if needed. Adjust engine RPM to recommended levels. |
– Vibrations and rattling noises | – Tighten any loose bolts and secure all components properly. | |
5. Electric Shock from Generator | – Users experiencing electric shocks | – Immediately disconnect the generator from the power source. Inspect and repair any damaged wiring or outlets. |
– Tingling sensation when touching the generator | – Check for grounding issues and ensure the generator is properly grounded. | |
6. Smoke Emission | – Visible smoke during operation | – Examine the oil level and quality. Change oil if it appears dirty or insufficient. |
– Unpleasant burning smell | – Inspect the air filter for clogs and replace if necessary. | |
7. Fuel Leaks | – Noticeable fuel odors or wet spots around the generator | – Check the fuel lines and connections for leaks. Replace any damaged components. |
– Decreased fuel efficiency | – Tighten loose fuel fittings and ensure the fuel tank is securely sealed. | |
8. Battery Issues | – Difficulty starting the generator | – Inspect the battery for corrosion or loose connections. Replace if necessary. |
– Weak or dead battery | – Charge or replace the battery as needed. | |
9. Generator Running Rough | – Uneven or shaky operation – Check the air-fuel mixture; adjust the carburetor to ensure the correct ratio. Inspect for clogged fuel injectors. | – Fluctuating RPMs – Inspect the ignition system for issues. Replace faulty spark plugs or ignition coils as necessary. |
Addressing these common generator issues promptly will help maintain the reliability of your power source. If problems persist, consider seeking professional assistance for more complex diagnostics and repairs.
Generator Maintenance Tips
Power outages can strike unexpectedly, making a well-maintained generator crucial for ensuring a continuous power supply. Regular maintenance not only enhances longevity but also guarantees optimal performance. Here are some key tips to keep your generator in top shape:
- Scheduled Inspections: Conduct routine checks on your generator to identify any signs of wear, loose connections, or potential issues before they escalate.
- Fluid Levels: Regularly check and replenish the oil and fuel levels to guarantee efficient operation. Proper lubrication is essential for preventing friction-related damage.
- Battery Health: Ensure the generator’s battery is charged and in good condition. A healthy battery is vital for a swift start when power is needed.
- Air Filter Checks: Keep the generator’s air filter clean and replace it as recommended by the manufacturer. A clogged filter can compromise performance and fuel efficiency.
- Coolant System Inspection: Verify the coolant levels and inspect the system for leaks. Overheating can lead to severe damage, so maintaining the right coolant levels is crucial.
- Capacitor Maintenance: Check and test the generator’s capacitors regularly. Faulty capacitors can lead to electrical issues, affecting the generator’s ability to produce a consistent power output.
- Run the Generator Regularly: Regularly starting the generator, even if it’s not in use, helps keep the engine components lubricated and prevents fuel system issues.
- Storage Considerations: If the generator is stored for an extended period, use a fuel stabilizer to prevent fuel deterioration. Empty the fuel tank or run the generator dry before storage to avoid gumming.
By adhering to these maintenance tips, you’ll ensure that your generator is ready to provide reliable power when you need it the most.
Generator Safety Tips
Generators are indispensable for providing power during outages, but ensuring their safe operation is paramount. Here are essential Generator Safety Tips to keep in mind:
- Proper Ventilation: Always operate generators in well-ventilated areas to prevent the buildup of harmful gases like carbon monoxide.
- Read the Manual: Familiarize yourself with the manufacturer’s guidelines for your specific generator model to understand its unique safety requirements.
- Regular Maintenance: Conduct routine checks on the generator, including fuel lines, filters, and oil levels, to guarantee optimal performance and identify potential issues early.
- Keep Flammable Materials Away: Position the generator away from flammable materials to reduce the risk of fire hazards.
- Carbon Monoxide Alarms: Install and regularly test carbon monoxide detectors near the generator area to provide an early warning of any dangerous gas levels.
- Grounding: Ensure proper grounding of the generator to prevent electrical shocks and protect both the equipment and users.
- Fuel Safety: Store fuel in approved containers, away from heat sources, and follow guidelines for proper storage to avoid spills and contamination.
- Emergency Shutdown: Understand and practice the emergency shutdown procedures to swiftly respond to potential dangers.
- Children and Pets: Keep children and pets away from the generator during operation to prevent accidents and injuries.
- Avoid Overloading: Respect the generator’s rated capacity and avoid overloading it to maintain efficient and safe operation.
- Cooling Time: Allow the generator to cool down before refueling to prevent accidental fires or burns. Follow the recommended cooldown period specified in the manual.
- Secure Placement: Place the generator on a stable, flat surface to prevent tipping and ensure safe operation. Avoid placing it on uneven or sloped terrain.
- Regular Testing: Periodically run the generator to ensure it starts easily and operates smoothly. This practice helps identify potential issues before they become major problems during an emergency.
- Extension Cord Safety: If using extension cords, ensure they are of sufficient gauge for the load and in good condition. Overloading cords can lead to overheating and pose a fire risk.
- Weather Considerations: Shelter the generator from the elements to protect it from rain and snow. Use appropriate covers or enclosures designed for your specific generator model.
- Professional Inspection: Schedule regular professional inspections to check for hidden issues and ensure all components are in good working order. This is especially important for standby generators.
- Emergency Services Awareness: Familiarize yourself with the location of emergency shut-off switches and how to quickly contact relevant services in case of a malfunction or emergency.
- Storage Precautions: If the generator is not in use for an extended period, follow proper storage procedures. This includes draining the fuel, disconnecting the battery, and storing it in a dry, cool place.
- Educate Users: Ensure that anyone who may need to operate the generator is familiar with its safety features and operation. Provide clear instructions to prevent accidents caused by misuse.
- Legal Compliance: Be aware of and adhere to local regulations regarding generator usage, emissions, and noise levels. Non-compliance may result in fines or other penalties.
Remember, adhering to these Generator Safety Tips is crucial to ensure the reliable and secure use of your generator.
Conclusion
In conclusion, How Much Copper Is in a Generator? shines a spotlight on the fundamental role of copper in the realm of power generation. As an essential conductor of electricity, copper enables generators to efficiently convert mechanical energy into the electrical power we rely on daily.
The amount of copper varies across generator types, with different technologies harnessing this metal’s conductivity to varying degrees. Embrace the beauty of the interplay between technology and materials, as you appreciate the significance of copper in fueling the electrifying future ahead.
References
- Electrical generators for large wind turbine: Trends and challenges
- Bio-inspired water-driven electricity generators: From fundamental mechanisms to practical applications
- Power electronic drives, controls, and electric generators for large wind turbines–an overview
- Stabilization of two electricity generators
Frequently Asked Questions
What are the different types of generators available in the market?
There are several types of generators available in the market, each with its unique features. These include portable generators, standby generators, inverter generators, and diesel generators. Each type caters to different power requirements and usage scenarios.
How does the price of copper affect the overall cost of a generator?
The price of copper significantly affects the overall cost of generator production. Fluctuations in copper prices can impact manufacturing expenses, particularly when copper is scarce, which increases costs and hampers efficient generator production processes.
Are there any alternative materials to copper that can be used in generators?
Alternative materials to copper, such as aluminum or superconductors, can be used in generators. Efficiency comparison studies have shown that these materials have the potential to reduce costs and improve performance, making them viable alternatives in generator construction.
What are the maintenance requirements for copper components in a generator?
Maintenance requirements for copper components in a generator include regular cleaning, lubrication, and inspection for signs of corrosion or wear. Proper storage and handling are also essential to prevent damage. Neglecting maintenance can lead to decreased efficiency and potential breakdowns.
How does the copper content in a generator impact its overall performance?
The copper content in a generator significantly impacts its overall performance. Copper’s high conductivity allows for efficient energy transfer, while its durability ensures the longevity of the generator’s components, contributing to reliable and consistent operation.
Do generators contain copper?
Generators indeed contain copper. The process involves utilizing electromagnetic principles to convert mechanical energy into electric current. This is achieved through the use of large stators and rotors wound with copper.
How do you scrap a generator?
To scrap a generator, one can start by calling local scrap yards to compare prices. Once the best location is determined, the generator can be disassembled. Afterward, it can be transported to the chosen scrap yard. It’s often possible to break down the generator and take it to the scrap yard on the same day.
How do you calculate the weight of copper in a generator?
To calculate the weight of copper in a generator, measure the length of each copper wire used in the armature and multiply it by the number of wires. Then, multiply the weight per unit length by the total length of copper wire to determine the overall weight of copper in the armature, measured in grams.