In a world buzzing with technological choices, the question on everyone’s mind is, can you parallel non inverter generators? It’s a query that resonates with those seeking power solutions without the intricate complexities of inverter models. Picture this: you, the outdoors enthusiast, yearning for a seamless power boost during camping adventures or backyard gatherings.
Imagine the convenience of combining the rugged reliability of non-inverter generators to meet your energy needs with ease. This curiosity is not just about connecting machines; it’s about intertwining convenience and power, harmonizing your energy desires. Let’s explore the possibilities that lie in the realm of parallel non-inverter generators and unlock a world where simplicity and effectiveness collide.
Jump to a Specific Section
- 1 Main Highlights
- 2 What are Non-Inverter Generators?
- 3 What is Paralleling?
- 4 Why Should You Parallel Two Generators?
- 5 Can You Parallel Non Inverter Generators?
- 6 Factors to Consider While Paralleling Two Generators
- 7 How to Parallel Non Inverter Generators?
- 8 Pros and Cons of Paralleling Non-inverter Generators
- 9 Risks of Paralleling Non-Inverter Generators
- 10 Why Non-Inverter Generators May Not be Suitable for Parallel Operation?
- 11 Troubleshooting Common Generator Issues
- 12 Generator Maintenance Tips
- 13 Generator Safety Tips
- 14 Conclusion
- 15 References
- 16 Frequently Asked Questions
- 16.1 What is the cost of paralleling non inverter generators?
- 16.2 Are there any safety considerations when paralleling non inverter generators?
- 16.3 Is there a limit to the number of non inverter generators that can be paralleled?
- 16.4 Are there any environmental considerations when paralleling non inverter generators?
- 16.5 Is there a specific type of non inverter generator that is best suited for parallel operation?
- 16.6 Can you connect two non inverter generators together?
- 16.7 Can you put 2 generators in parallel?
- 16.8 Can you parallel different size Generac generators?
Main Highlights
- Paralleling non-inverter generators can increase power output, fuel efficiency, and reduce emissions, but careful planning and preparation are required.
- Professional electrician consultation is essential prior to attempting a paralleling setup.
- Safety considerations must always be taken into account when connecting any type of generator together, and durability issues and higher maintenance costs may arise when operating multiple non-inverter generators in parallel.
- Mismatching frequencies can cause damage to either the engines or connected loads, and not all non-inverter generators have been designed with the capability of being run in parallel.
What are Non-Inverter Generators?
Non-Inverter Generators, also known as conventional or standard generators, operate on a simple and straightforward principle. These generators produce AC (alternating current) power, providing a reliable source of electricity for various applications. Unlike their counterpart, inverter generators, non-inverter generators don’t have the advanced electronic components for power modulation.
- Stable Power Output: One of the defining features of non-inverter generators is their consistent power output. They are well-suited for running traditional appliances and tools that don’t require precise voltage and frequency.
- Cost-Effective: Non-inverter generators are often more budget-friendly than their inverter counterparts. This makes them an attractive option for individuals or businesses with basic power needs.
- Noisy Operation: While effective, non-inverter generators tend to be louder during operation. The constant RPM (revolutions per minute) contributes to a higher noise level, which can be a consideration in noise-sensitive environments.
- Heavy and Bulky: In terms of portability, non-inverter generators are typically heavier and bulkier than inverter models. This can make them less convenient for activities such as camping or tailgating.
What is Paralleling?
Generator paralleling is a critical aspect of power systems, contributing significantly to the efficiency and reliability of power generation. In essence, generator paralleling involves the synchronization and simultaneous operation of multiple generators to meet varying power demands seamlessly.
Generators are devices that convert mechanical energy into electrical energy, and when their outputs are paralleled, the combined power output becomes greater than that of a single generator. This process is especially valuable in situations where a single generator may not suffice to meet the power requirements, such as in large industrial facilities, data centers, or events.
Synchronization is a key element in generator paralleling. It ensures that the voltage, frequency, and phase of each generator are in perfect harmony, allowing them to operate together efficiently. Modern generator paralleling systems often employ advanced technologies, including sophisticated control systems and communication protocols, to achieve precise synchronization.
The benefits of generator paralleling are manifold. Firstly, it provides enhanced reliability by distributing the load among multiple generators, reducing the risk of a single point of failure. Secondly, it allows for more flexibility in managing power demands. As the load increases or decreases, additional generators can be brought online or taken offline, optimizing fuel efficiency and overall system performance.
Why Should You Parallel Two Generators?
When considering power generation, the option to parallel two generators emerges as a strategic choice for various reasons. One of the primary advantages lies in increased power output. By connecting two generators in parallel, you effectively combine their individual capacities, resulting in a higher overall power output. This can be particularly beneficial in situations where a single generator may not meet the power demands adequately.
Improved Redundancy is another key factor. Parallel operation provides a built-in backup system. In case one generator experiences a malfunction or requires maintenance, the parallel configuration ensures that the second generator can seamlessly take over the load. This enhanced reliability is crucial, especially in critical applications where uninterrupted power is paramount.
Furthermore, parallel operation facilitates load sharing between the generators. This means that the power demand is distributed more evenly between the units, promoting efficient use of resources. The ability to share the load ensures that neither generator is overworked, leading to improved performance and longevity.
In addition to scalability and reliability, the parallel configuration also offers flexibility in managing power demand fluctuations. As demand increases, additional generators can be easily brought online and synchronized in parallel to meet the rising requirements. Conversely, when demand decreases, generators can be taken offline, optimizing fuel efficiency and reducing operational costs.
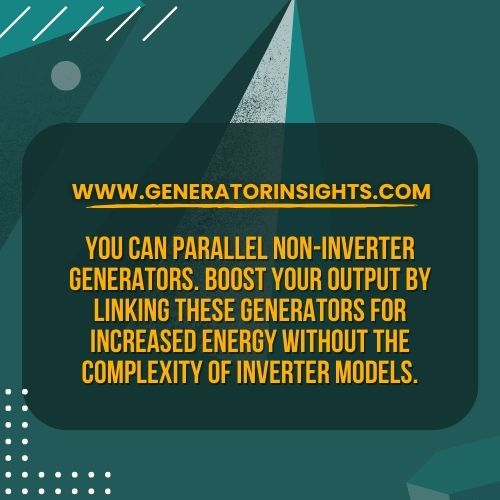
Can You Parallel Non Inverter Generators?
Combining multiple power sources can be a great way to boost output, but it’s important to ensure compatibility before attempting to parallel non-inverter generators. While you can parallel non-inverter generators, not all non-inverters can be paralleled.
When paralleling, all of the generators must be correctly sized and maintained in order for them to achieve peak efficiency. This includes checking the fuel efficiency, noise output, power output, voltage regulation and surge protection.
Additionally, connection cables must be used to connect the power sources together and load balancing must also be taken into account when storing electricity between the two or more sources.
It is possible to parallel non-inverter generators so long as they are properly configured for the task. As such, it is important that a professional electrician is consulted prior to attempting any kind of paralleling setup in order to make sure all safety protocols are followed and that the necessary steps have been taken for a successful installation.
Furthermore, any system should be tested thoroughly after installation in order to verify that everything is connected properly and working as intended with no issues.
Paralleling multiple non-inverter generators provides many benefits including increased reliability through redundancy and improved power output capabilities over just one single generator alone; however, proper care must still be taken during each step of the process from generator sizing and maintenance through load balancing for optimal performance.
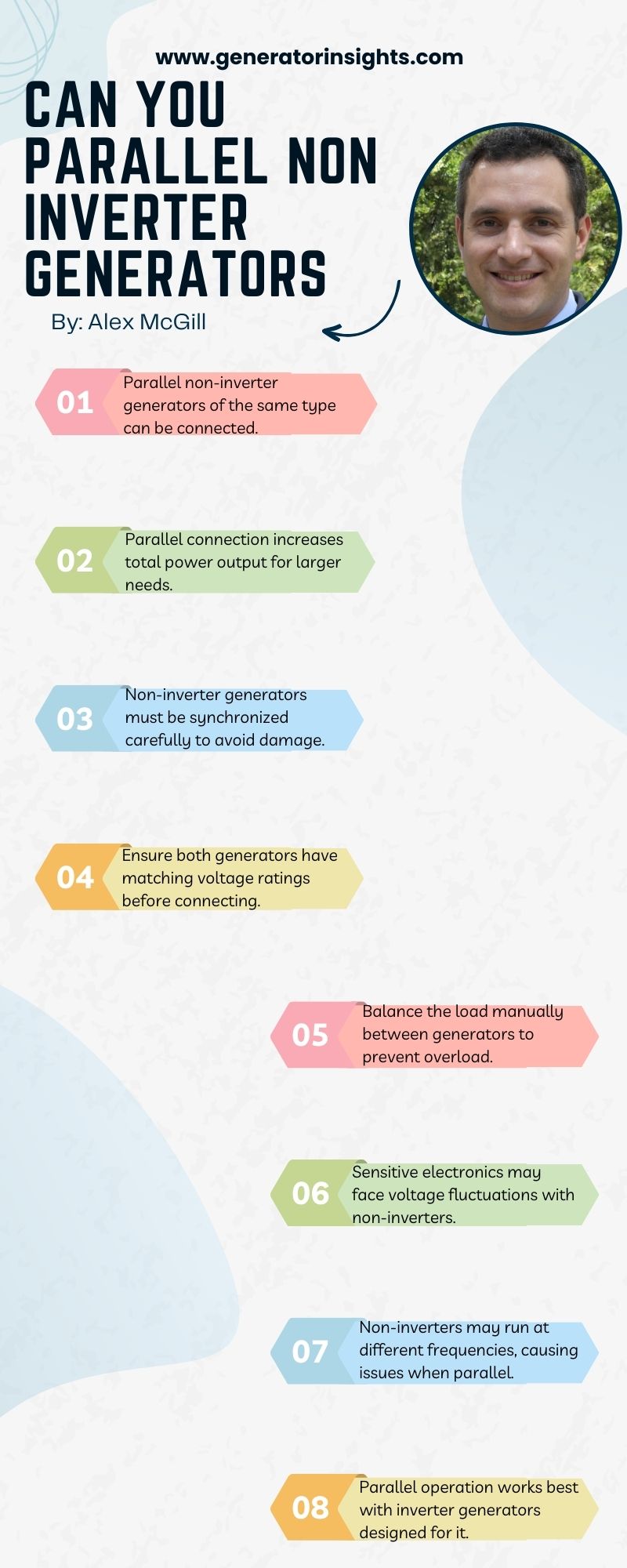
Factors to Consider While Paralleling Two Generators
When paralleling two generators, it’s crucial to ensure a seamless and efficient power supply. This process involves connecting two or more generators to work in tandem. Consider the following factors for a successful parallel operation:
- Generator Compatibility:
- Ensure that the generators have similar voltage, frequency, and phase sequence. Any discrepancies can lead to instability in the parallel operation.
- Synchronization:
- Governor Settings:
- Adjust the governor settings to maintain uniform speed control. This prevents one generator from taking on a disproportionate load, ensuring a balanced distribution.
- Load Sharing Mechanism:
- Implement a robust load-sharing mechanism to distribute the electrical load evenly between the generators. This is essential for preventing overloading and optimizing efficiency.
- Protection Systems:
- Install comprehensive protection systems to detect faults or irregularities promptly. This includes overcurrent protection, under-frequency protection, and other safety measures.
- Communication Systems:
- Establish effective communication systems between the generators. This facilitates real-time sharing of data, enabling quick adjustments and responses to changes in load or system conditions.
- Islanding Protection:
- Implement islanding protection to detect and disconnect the generators if they continue to operate independently of the main power grid. This enhances overall system safety.
- Testing and Maintenance:
- Regularly conduct thorough testing and maintenance of the parallel operation setup. This ensures that all components are functioning correctly and helps identify any potential issues in advance.
With these considerations kept in mind it is certainly possible to realize powerful results by safely paralleling non-inverter generators.
How to Parallel Non Inverter Generators?
Paralleling non-inverter generators can significantly enhance power output and provide a more reliable energy source. This process allows you to combine the capabilities of multiple generators to meet increased power demands.
Parallel operation is especially useful in scenarios where a single generator may fall short. Below, we’ll guide you through the step-by-step process of parallelizing non-inverter generators.
Step 1: Choose Compatible Generators
Before attempting to parallelize generators, it’s crucial to ensure they are compatible. Generator compatibility involves matching the voltage, frequency, and phase of each unit. Verify the manufacturer’s specifications and guidelines to guarantee seamless parallel operation.
Step 2: Gather Necessary Equipment
To parallelize non-inverter generators, you’ll need a parallel kit or a suitable paralleling switchgear. These devices enable safe and efficient connection of multiple generators. Ensure you have the necessary cables, connectors, and safety equipment before proceeding.
Step 3: Prepare Generators for Parallel Operation
Start by shutting down all the generators. Connect the parallel kit or switchgear to each generator following the manufacturer’s instructions. Pay special attention to the correct connection of phase and neutral conductors to avoid issues during parallel operation.
Step 4: Adjust Generator Settings
Access the control panels of each generator and set the parameters for parallel operation. This includes configuring voltage and frequency settings. Make sure to consult the generator manuals for specific instructions on adjusting these settings.
Step 5: Start Generators in Parallel
With all settings adjusted, start each generator individually and ensure they reach a stable operating condition. Once stabilized, use the parallel kit or switchgear to connect the generators. Monitor the combined output to confirm that the generators are working in parallel without any issues.
Step 6: Load Distribution
Distribute the load evenly across the parallelized generators. This can be done manually or, in some cases, the generators may have an automatic load-sharing feature. Balancing the load ensures optimal performance and prevents overloading of any individual generator.
Step 7: Shutdown Procedure
When you’re finished using the parallelized generators, follow the proper shutdown procedure. Disconnect the generators using the parallel kit or switchgear and shut down each generator individually. This helps maintain the longevity of the equipment and ensures a safe operation.
Thus, paralleling non-inverter generators requires careful consideration of compatibility and adherence to manufacturer guidelines. Following these step-by-step instructions will enable you to harness the combined power of multiple generators efficiently and reliably. Always prioritize safety and consult the manufacturer’s documentation for specific details related to your generators.
You can read about how to parallel two portable generators here. Moreover, if you want to know the difference between inverters and traditional generators, we highly recommend you read our guide here.
Pros and Cons of Paralleling Non-inverter Generators
When considering power generation options, it’s crucial to weigh the advantages and disadvantages of different setups. Let’s delve into the pros and cons of this approach.
In summary, the decision to parallel non-inverter generators depends on specific requirements and constraints. Understanding these pros and cons is crucial for making informed choices in power generation setups.
Risks of Paralleling Non-Inverter Generators
Here are risks associated with paralleling non-inverter generators:
Risk Factor | Description |
---|---|
Voltage Fluctuations | Paralleling non-inverter generators may lead to unstable voltage levels, impacting sensitive electronic equipment. |
Frequency Mismatch | Combining generators without synchronization can result in frequency mismatches, causing operational issues and potential damage. |
Poor Load Sharing | Non-inverter generators may struggle with uneven load distribution, leading to some generators working harder than others. |
Limited Control Capabilities | Lack of advanced control features in non-inverter generators can hinder precise adjustments, affecting overall system performance. |
Increased Fuel Consumption | Inefficient load management may lead to higher fuel consumption, reducing the cost-effectiveness of the power generation system. |
Voltage Instability during Transients | Paralleling non-inverter generators might experience voltage instability during load changes or transients, impacting connected devices. |
Harmonics and Power Quality Issues | Non-inverter generators may produce harmonics and poor power quality, potentially causing disruptions in sensitive electronic systems. |
With this understanding in mind, let’s explore why some non-inverter generators may not be suitable for parallel operation?
Why Non-Inverter Generators May Not be Suitable for Parallel Operation?
When considering the operation of generators in parallel, it’s crucial to understand the factors that make non-inverter generators less suitable for this configuration. Let’s delve into the reasons why parallel operation may pose challenges with non-inverter generators.
- Output Fluctuations:
- Non-inverter generators tend to have less stable power output, leading to fluctuations that can disrupt the parallel operation.
- These fluctuations can result in mismatches between generators, causing issues with the overall power supply.
- Voltage and Frequency Variability:
- In a parallel setup, maintaining consistent voltage and frequency is paramount.
- Non-inverter generators may struggle to synchronize these crucial parameters, impacting the stability of the entire power system.
- Limited Load Handling Precision:
- Achieving precise load sharing is essential for parallel operation.
- Non-inverter generators may lack the fine-tuned load handling capabilities found in their inverter counterparts, leading to imbalances.
- Sensitive Electronics Risk:
- Parallel operation often involves powering sensitive electronic devices or systems.
- The inherent voltage and frequency fluctuations in non-inverter generators can pose a risk to these electronics, potentially causing damage.
- Inefficient Fuel Consumption:
- Parallel operation is optimized when generators can efficiently share loads, promoting fuel efficiency.
- Non-inverter generators might struggle with load variations, leading to suboptimal fuel consumption and increased operational costs.
Troubleshooting Common Generator Issues
Generators are indispensable during power outages, ensuring a continuous power supply. However, users may encounter issues that hinder their optimal performance. Below is a comprehensive guide to troubleshoot common generator issues and restore seamless operation.
Issue | Symptoms | Troubleshooting Steps |
---|---|---|
1. Engine Fails to Start | – Silent operation | – Check fuel levels and ensure there’s an adequate supply. |
– Starter motor cranks but fails to ignite | – Inspect the spark plug for signs of damage or wear. Replace if necessary. | |
– Strong smell of gasoline | – Examine the carburetor for blockages and clean or replace if needed. | |
2. Low Power Output | – Dimming lights and fluctuating power output | – Verify the load capacity and ensure it doesn’t exceed the generator’s limit. |
– Appliances not running at full capacity | – Inspect the voltage regulator for malfunctions and replace if necessary. | |
3. Generator Overheating | – Unusual heat emanating from the generator | – Check the cooling system, including the radiator and coolant levels. Clean or replace components as required. |
– Frequent shutdowns due to overheating | – Ensure proper ventilation around the generator and clean any debris obstructing airflow. | |
4. Excessive Noise Levels | – Unusual or loud sounds during operation | – Inspect the muffler for damage and replace if needed. Adjust engine RPM to recommended levels. |
– Vibrations and rattling noises | – Tighten any loose bolts and secure all components properly. | |
5. Electric Shock from Generator | – Users experiencing electric shocks | – Immediately disconnect the generator from the power source. Inspect and repair any damaged wiring or outlets. |
– Tingling sensation when touching the generator | – Check for grounding issues and ensure the generator is properly grounded. | |
6. Smoke Emission | – Visible smoke during operation | – Examine the oil level and quality. Change oil if it appears dirty or insufficient. |
– Unpleasant burning smell | – Inspect the air filter for clogs and replace if necessary. | |
7. Fuel Leaks | – Noticeable fuel odors or wet spots around the generator | – Check the fuel lines and connections for leaks. Replace any damaged components. |
– Decreased fuel efficiency | – Tighten loose fuel fittings and ensure the fuel tank is securely sealed. | |
8. Battery Issues | – Difficulty starting the generator | – Inspect the battery for corrosion or loose connections. Replace if necessary. |
– Weak or dead battery | – Charge or replace the battery as needed. | |
9. Generator Running Rough | – Uneven or shaky operation – Check the air-fuel mixture; adjust the carburetor to ensure the correct ratio. Inspect for clogged fuel injectors. | – Fluctuating RPMs – Inspect the ignition system for issues. Replace faulty spark plugs or ignition coils as necessary. |
Addressing these common generator issues promptly will help maintain the reliability of your power source. If problems persist, consider seeking professional assistance for more complex diagnostics and repairs.
Generator Maintenance Tips
Power outages can strike unexpectedly, making a well-maintained generator crucial for ensuring a continuous power supply. Regular maintenance not only enhances longevity but also guarantees optimal performance. Here are some key tips to keep your generator in top shape:
- Scheduled Inspections: Conduct routine checks on your generator to identify any signs of wear, loose connections, or potential issues before they escalate.
- Fluid Levels: Regularly check and replenish the oil and fuel levels to guarantee efficient operation. Proper lubrication is essential for preventing friction-related damage.
- Battery Health: Ensure the generator’s battery is charged and in good condition. A healthy battery is vital for a swift start when power is needed.
- Air Filter Checks: Keep the generator’s air filter clean and replace it as recommended by the manufacturer. A clogged filter can compromise performance and fuel efficiency.
- Coolant System Inspection: Verify the coolant levels and inspect the system for leaks. Overheating can lead to severe damage, so maintaining the right coolant levels is crucial.
- Capacitor Maintenance: Check and test the generator’s capacitors regularly. Faulty capacitors can lead to electrical issues, affecting the generator’s ability to produce a consistent power output.
- Run the Generator Regularly: Regularly starting the generator, even if it’s not in use, helps keep the engine components lubricated and prevents fuel system issues.
- Storage Considerations: If the generator is stored for an extended period, use a fuel stabilizer to prevent fuel deterioration. Empty the fuel tank or run the generator dry before storage to avoid gumming.
By adhering to these maintenance tips, you’ll ensure that your generator is ready to provide reliable power when you need it the most.
Generator Safety Tips
Generators are indispensable for providing power during outages, but ensuring their safe operation is paramount. Here are essential Generator Safety Tips to keep in mind:
- Proper Ventilation: Always operate generators in well-ventilated areas to prevent the buildup of harmful gases like carbon monoxide.
- Read the Manual: Familiarize yourself with the manufacturer’s guidelines for your specific generator model to understand its unique safety requirements.
- Regular Maintenance: Conduct routine checks on the generator, including fuel lines, filters, and oil levels, to guarantee optimal performance and identify potential issues early.
- Keep Flammable Materials Away: Position the generator away from flammable materials to reduce the risk of fire hazards.
- Carbon Monoxide Alarms: Install and regularly test carbon monoxide detectors near the generator area to provide an early warning of any dangerous gas levels.
- Grounding: Ensure proper grounding of the generator to prevent electrical shocks and protect both the equipment and users.
- Fuel Safety: Store fuel in approved containers, away from heat sources, and follow guidelines for proper storage to avoid spills and contamination.
- Emergency Shutdown: Understand and practice the emergency shutdown procedures to swiftly respond to potential dangers.
- Children and Pets: Keep children and pets away from the generator during operation to prevent accidents and injuries.
- Avoid Overloading: Respect the generator’s rated capacity and avoid overloading it to maintain efficient and safe operation.
- Cooling Time: Allow the generator to cool down before refueling to prevent accidental fires or burns. Follow the recommended cooldown period specified in the manual.
- Secure Placement: Place the generator on a stable, flat surface to prevent tipping and ensure safe operation. Avoid placing it on uneven or sloped terrain.
- Regular Testing: Periodically run the generator to ensure it starts easily and operates smoothly. This practice helps identify potential issues before they become major problems during an emergency.
- Extension Cord Safety: If using extension cords, ensure they are of sufficient gauge for the load and in good condition. Overloading cords can lead to overheating and pose a fire risk.
- Weather Considerations: Shelter the generator from the elements to protect it from rain and snow. Use appropriate covers or enclosures designed for your specific generator model.
- Professional Inspection: Schedule regular professional inspections to check for hidden issues and ensure all components are in good working order. This is especially important for standby generators.
- Emergency Services Awareness: Familiarize yourself with the location of emergency shut-off switches and how to quickly contact relevant services in case of a malfunction or emergency.
- Storage Precautions: If the generator is not in use for an extended period, follow proper storage procedures. This includes draining the fuel, disconnecting the battery, and storing it in a dry, cool place.
- Educate Users: Ensure that anyone who may need to operate the generator is familiar with its safety features and operation. Provide clear instructions to prevent accidents caused by misuse.
- Legal Compliance: Be aware of and adhere to local regulations regarding generator usage, emissions, and noise levels. Non-compliance may result in fines or other penalties.
Remember, adhering to these Generator Safety Tips is crucial to ensure the reliable and secure use of your generator.
Conclusion
In conclusion of can you parallel non inverter generators we found that you can parallel non inverter generators. By paralleling two or more of these generators together, you can increase the available wattage and current capacity as needed. However, it is important to keep in mind that some non-inverter generators may not be suitable for this operation due to the risks involved.
Therefore, it is important to do your research and find out if the type of generator you have will allow for safe parallelization before attempting any kind of modification. If done correctly, paralleling non inverter generators can provide a useful way to increase power output for various applications.
References
- Should we use a portable generator in an emergency?
- Carbon monoxide poisoning from portable electric generators
- Active-passive control of portable generator set radiated noise
- Studies on control of noise from portable power generator
Frequently Asked Questions
What is the cost of paralleling non inverter generators?
The cost of paralleling non inverter generators depends on energy efficiency, noise levels, fuel consumption, sizing requirements, efficiency ratings, installation methods, start up procedures, maintenance requirements, load balancing and power output. Consider these factors when budgeting for your project.
Are there any safety considerations when paralleling non inverter generators?
Yes, there are safety considerations when paralleling non inverter generators. These include building safety, power management, noise control, fuel savings, connection requirements, wattage ratings, voltage compatibility, engine maintenance and wiring diagrams. Additionally exhaust regulations must be taken into account.
Is there a limit to the number of non inverter generators that can be paralleled?
Yes, there is a limit to the number of non inverter generators that can be paralleled. Factors such as power output, efficiency levels, synchronization process, fuel consumption, exhaust emissions, connection method, load sharing, noise pollution and voltage stability must be considered when assessing risk management.
Are there any environmental considerations when paralleling non inverter generators?
Yes, there are environmental considerations when paralleling non inverter generators. For better fuel efficiency and noise reduction, consider emissions control, air pollution, generator placement, power output and installation process. Maintenance requirements should also be taken into account along with fuel storage and power sharing.
Is there a specific type of non inverter generator that is best suited for parallel operation?
You should consider adapter compatibility, fuel consumption, noise levels, power capacity, maintenance requirements, portability, power reliability, emission levels, setup complexity and installation costs when deciding which type of non-inverter generator is best suited for parallel operation.
Can you connect two non inverter generators together?
Paralleling generators is a viable solution to increase power output by combining two individual non-inverter generators. This method, known as paralleling, allows the user to effectively double the wattage, enabling the powering of larger loads such as RV air conditioners using smaller units.
Can you put 2 generators in parallel?
Running two generators in parallel is feasible, irrespective of their model or size. However, it’s essential to consider and match the ratings for output voltage and frequency for each generator to ensure a seamless parallel operation.
Can you parallel different size Generac generators?
Paralleling different-sized Generac generators provides enhanced flexibility and redundancy, allowing multiple smaller generators to function collectively as a single, more powerful unit. Synchronization is crucial, requiring the control systems of the generators to communicate with each other to maintain optimal performance.